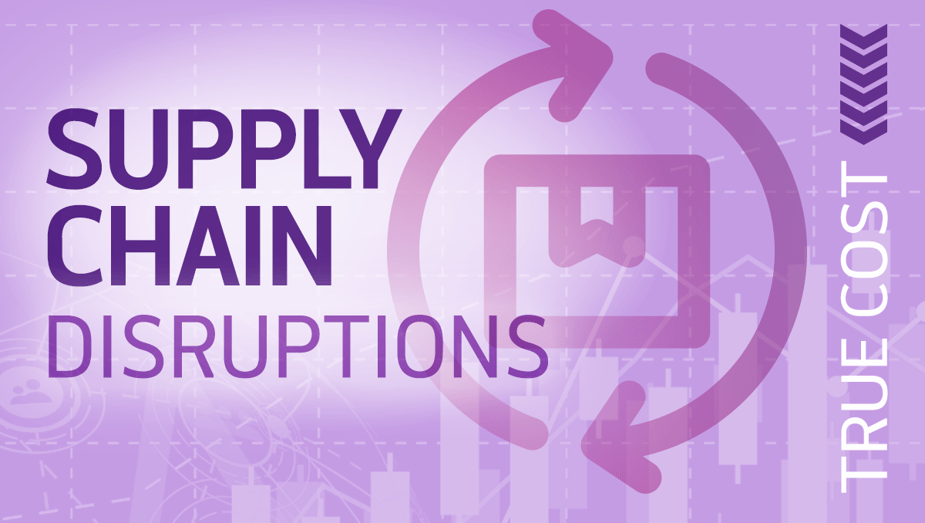
- Home
- PLM & Compliance Blog
- Measuring the true cost of supply chain disruptions and other business impacts
Measuring the true cost of supply chain disruptions and other business impacts
|
PLM
|
PLM For Food And Beverage
|
Supplier Relationship Management
Posted By:
Trace One
Despite efficiencies in global manufacturing, there are still major challenges up and down the supply chain.
The cumulative consequence of supply chain difficulties—which include everything from the availability of raw materials to the amount of time it takes to move product around the world, creates ripple effects.
And all these disruptions and uncertainties typically mean one thing: everything will cost more.
Four supply chain glitches increasing business costs
A multitude of factors, everything from tangible numbers—like the cost of fuel—to intangibles—like lost opportunity in the marketplace—can be attributed to the supply chain. These are externalities which no single individual can control, which is why supply chain is often a thorn in the side of manufacturers.
Here are four areas currently contributing to supply chain instability:
Worker shortages
Supplier delays have become routine for many manufacturers, due, in part, to a lack of critical workers, including truckers, warehouse employees, and factory staff. All of this reduces the amount of available materials, ultimately affecting the bottom line.
Transportation
Shipping delays are also a persistent problem.
When ships are gridlocked in faraway ports, the result is not just slower delivery—costs have increased ten-fold, anywhere between $5,000 to $25,000 per shipping container. Part of this is due to limited availability of shipping materials and crates, but a major backlog of trucks and cargo ships jamming up ports have been a factor as well.
Availability of materials
Wheat, sunflower oil, and corn are in short supply, partially due to Russia’s invasion of Ukraine. Not only does this drive the price up on crucial ingredients, it forces companies to reformulate recipes, creating additional strains on the availability of materials.
Inflation
Rising global inflation is impacting every facet of the supply chain, especially as customers pivot between restaurants and grocery retailers. Inflation and the supply chain can contribute to a vicious cycle, with rising costs impacting the supply chain, which only results in more inflation.
Controlling supply chain uncertainties with data
Data from disparate sources goes a long way in informing business decisions, especially when captured from different points along the supply chain.
But ingesting supplier data can result in a deluge of information, making it hard to determine what data to focus on and how to shape and build business strategy in the wake of supply chain bottlenecks, inflation, and other upheavals.
In a data-rich culture and economy, companies that make smart, data-driven decisions will deliver more business value than their competitors, and that’s key to combat the business impact of supply chain disruptions.
Trace One Devex PLM gives food manufacturers a clear understanding of true costs across the product lifecycle
Trace One Devex PLM for food & beverage helps food manufacturers stay attuned to rapidly shifting markets and manage product lifecycles by capturing data from suppliers, including availability of ingredients and associated costs.
From these insights food producers can take the appropriate steps to deliver products with agility. Data is no longer an added obstacle to calculating supply chain costs, but an advantage. Reformulations can be completed on the fly, complete with cost forecasting using the same supplier data informing availability of ingredients, packaging materials, or transportation.
Interested in finding out how Trace One Devex PLM can help your company? Schedule a demo today.