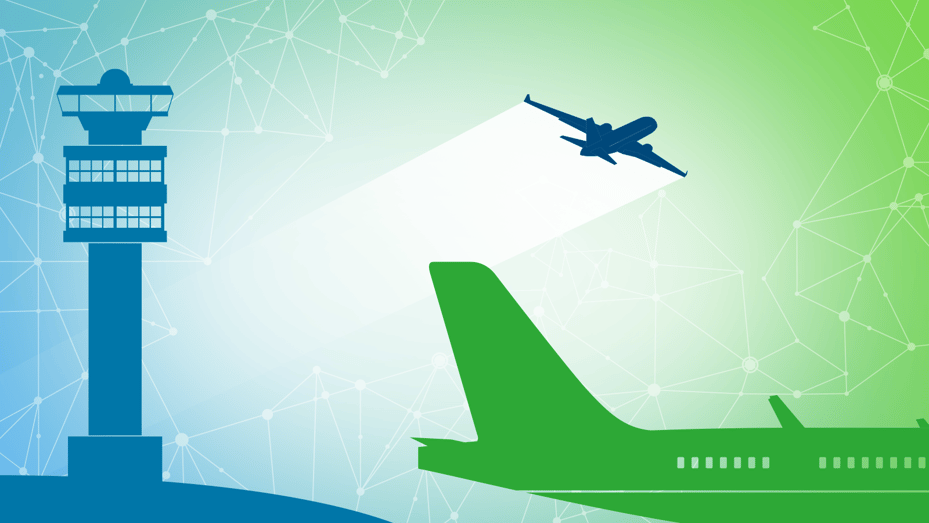
Customer’s Voice: Trace One Devex PLM lessons learned
|
Product Lifecycle Management
|
Food & Beverage
|
Supplier Relationship Management
Posted By:
Trace One
Editor's note: This is the eleventh post in our "Customer Voice" series where we capture and bring to you the direct voice of our customers to demonstrate their areas of PLM ROI. View the other posts below:
Gaining and Maintaining a Competitive Advantage
Launching Trace One Devex PLM in 8 Months
Integrating Trace One Devex PLM into a Single System
Using Trace One Devex PLM for Quality Assurance
How Trace One Devex PLM Improves Innovation
Creating Cross-functionality with Trace One Devex PLM
Using Trace One Devex PLM to Improve Project Work Efficiencies
How Business Process Reengineering Improved Workflows
How Trace One Devex PLM Contains Costs
Trace One Devex PLM and Formula Development Efficiency
PLM for visibility and traceability
With products in over 170 different markets, the largest private spirits company in the world relies on Trace One Devex PLM to manage packaging and new product development. A longtime Trace One client, the global brand has witnessed the benefit of Trace One Devex PLM firsthand.
“We have been doing our product formulation in Trace One Devex PLM for over 15 years,” says a New Product Development Manager in charge of product lifecycle management. “It’s been great watching Trace One Devex PLM become an entire PLM suite.”
The company uses Trace One Devex PLM for visibility and consistent data across collaborators. This approach allows them to stay agile and innovative. The efficiencies introduced by Trace One Devex PLM promote a proactive development strategy.
“We’re always looking at distribution channels and options that will be available within the next five years,” says the Development Manager.
Lessons from the latest implementation
Having experienced several iterations of Trace One Devex PLM and Trace One's offerings, the company rolled out a PLM to include the packaging workflows. With this upgrade, the company was able to create more efficient processes.
“We’ve learned a few things from our implementations,” notes the Development Manager. “The biggest lesson is this--it takes time.”
Onboarding correctly made a big difference in the long run. Several systems had to be integrated to improve workflow and ensure solutions could communicate.
“Packaging was a very successful implementation,” says the Development Manager. “Aligning data probably takes the longest time, and there were definitely challenges with legacy data, but we were well supported by Trace One.”
Aligning data removed silos and allowed systems to work in unison. Once these data points were able to communicate across systems, new and more efficient processes were introduced.
Lessons in efficiency
With 20 production facilities and around 6,000 employees, success requires consistent and accurate workflows. Using Trace One Devex PLM for packaging created a model where standards could be templated and replicated for new designs. This approach further supported collaboration and proper development practices.
“We have four stages for designing new packaging, from drafting to production,” remarks the Development Manager. “Each BOM uses the previous stage as a template and then builds things progressively. It’s very efficient and works well with our integrated PLM system.”
View our infographic The 4 types of BOMs Common in PLM
The company also leverages Trace One Devex PLM in the formulation of new product, removing manual steps and improving accuracy in the workflow. This allows the company to innovate in advance, anticipating what their market needs might be.
“All formula development storage, specification management, document storage, and knowledge management happen in Trace One Devex PLM,” says the Development Manager. “We need a five-year pipeline of things that are ready to go. We don’t always select a new product for launch, but it’ll be available if we want to go back.”
Since Trace One Devex PLM is capable of controlling access based on role, the company uses the solution’s status settings to determine when a formula will be made available to plants.
“Considering that all formulas can be in Trace One Devex PLM for years and just need a status change, we can remove a lot of the manual steps of transferring data back and forth,” notes the Development Manager. “If systems aren’t communicating, you risk becoming a convoluted process with a lot of obsolete or depleted information.”
Lessons for the future
Having relied on Trace One Devex PLM for product lifecycle management for so long, the company eagerly looks forward to adopting new efficiencies and functionalities, including supplier collaboration and sustainability efforts.
“There’s a lot we want to do with the Supplier Portal in Trace One Devex PLM,” says the Development Manager. “It will eliminate most of the spreadsheets being used at the moment.”
The Trace One Devex PLM Supplier Collaboration Portal not only supports vendor management, it standardizes data that moves between partners. This helps to improve the quality and accuracy of data, especially for companies that rely on multiple suppliers.
The company is also considering Trace One’s sustainability offering, Trace One Sustainability.
“Packaging is an obvious area for sustainability,” notes the Development Manager. “There are more options here, but also opportunities in water and waste treatment from plants.”
Trace One Sustainability allows companies to capture data on environmental impacts and improve sustainability.
A long partnership with Trace One has helped support efficient and profitable practices. Stages have more visibility and oversight, and team members are capable of innovating holistically, improving workflows for packaging and formula development.