Defining Discrete vs. Process Manufacturing in Retail PLM
Discrete and process manufacturing differ in fundamental ways.
- Discrete manufacturing unites components into individual units of product by routing them through a sequence of assembly.
- Process manufacturing combines raw materials and ingredients into batches of product by following a recipe or formulation.
Discrete Manufacturing |
Process Manufacturing |
Produces individual units |
Produces batches or quantities |
Routed through sequential or parallel assembly |
Created through mixing, blending, combining, or reacting |
Constructed of parts, components, and sub-assemblies |
Ingredients combined by quantity |
Directed by a bill of materials (BOM) |
Determined by a recipe or formula in addition to BOMs |
Assembled in work centers |
Combined in manufacturing plants |
Units of measure: parts |
Units of measure: Weight or volume |
Reversible assembly |
Irreversible combination |
What Is Discrete Manufacturing?
Discrete manufacturing assembles final products that represent distinct, individual units. These could be as simple as a fastener or as complex as a smartphone or aircraft.
There are several core elements involved in discrete manufacturing:
- A bill of materials (BOM) represents all the individual parts or components that make up a discrete unit of product. Some components require advance manufacturing into sub-assemblies. In those cases, multi-level or layered BOMs help manage complexity.
- Work centers are the individual locations or stations where assembly takes place. These could constitute one workstation, a set of them, or an entire production line specialized to handle one aspect of manufacturing.
- The sequence of assembly defines the workflow that leads to the final product. It can pass through various work centers either sequentially or in parallel in a process known as production routing. The complexity of the sequence depends on the type of workflow, for example, mass production, batch production, or job shop.
- Assembly and disassembly are common features of discrete products, unlike the outputs of process manufacturing. For example, you can generally assemble, disassemble, and reassemble consumer electronics, but you typically can’t de-constitute a finished chemical compound.
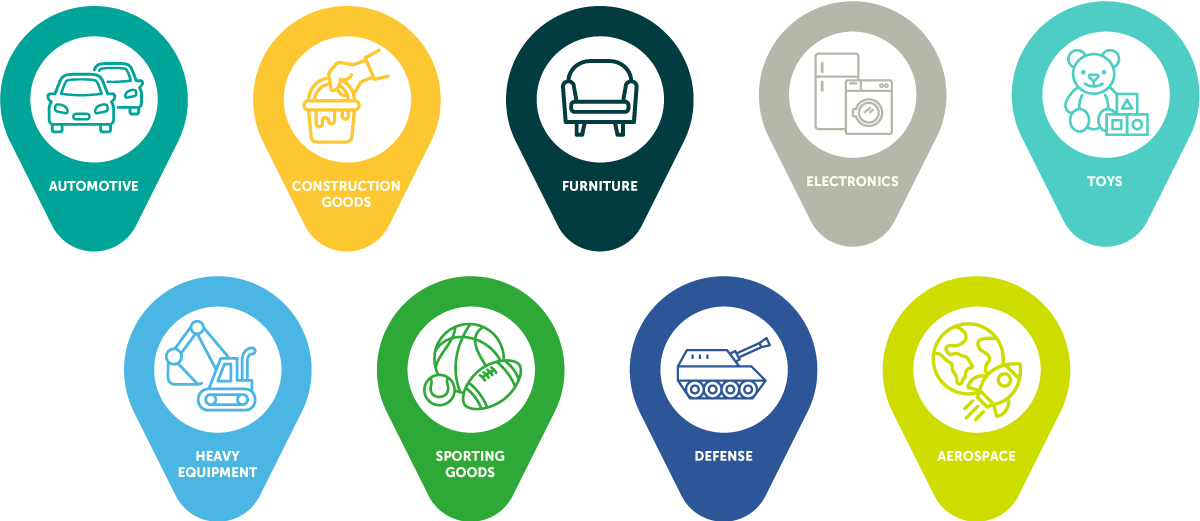
Outline of the Discrete Manufacturing Process
The sequence of assembly is only one part of a much wider process that involves many different disciplines and areas of expertise.
A Garlic Press Takes Shape
To get a sense of discrete manufacturing in action, imagine the creation of a garlic press that retailers will sell alongside consumer packaged goods (CPG) in a supermarket.
- Design: First, designers create the garlic press’s blueprint and specifications, which involve detailed engineering and computer-aided design (CAD) systems. In this case, the garlic press needs two handles, a hinge assembly, and a detachable hopper and screen.
- Planning: Now, the team determines what materials, equipment, and resources the product needs, then maps out an assembly process, schedules production timelines, and estimates its costs.
- Procurement: The manufacturer will fabricate the handles and hopper, and purchase the hinge sub-assembly from a supplier. Acquiring the raw materials and components requires careful navigation of supplier relationships and delivery schedules.
- Production: The manufacturer implements production across work centers responsible for molding and machining the handles and hopper, with another center dedicated to attaching the hinge subassembly.
- Quality Control: Inspecting the product ensures each unit meets the required specifications and standards. A dedicated onsite department handles this process through random testing.
- Packaging: Preparing the product for storage and shipment is the final physical stage in the production process. The manufacturer decides to use window box packaging to offer visibility while keeping the product sanitary. It establishes a work center to handle this step.
A Discrete Manufacturing Process Flow Chart
How Discrete Manufacturers Use PLM Software
Discrete manufacturing is inherently complex and challenging. A comprehensive discrete manufacturing software solution helps producers manage their portfolios, eliminate waste, and accelerate production.
Industry Challenge |
PLM Solutions |
Supply chain management in changing global markets is increasingly complex and difficult to optimize. |
PLM solutions feature supplier management tools to help manufacturers procure raw materials and components directly from the global marketplace so they can maintain a stable and flexible supply chain. |
Managing BOMs involves mountains of information that demand rigorous organization to keep assembly on track. |
Integrated and automated BOM production enables the creation of material masters within ERP systems so manufacturers can avoid third-party integrations or human error during information transfer. |
Product portfolios and all of their related data can be difficult to manage, especially as new products enter and exit a manufacturer’s catalog. |
Innovation software unites process intelligence with product analysis to help manufacturers manage and optimize their entire product portfolios in one place. |
Product packaging represents a difficult balance of cost, branding, quality, consumer preferences, and environmental impact. |
Packaging management solutions support adherence to new regulations and help producers meet consumer expectations for sustainable packaging design. |
Environmental sustainability requires strict adherence to a rapidly evolving regulatory compliance ecosystem, along with careful monitoring for processes and materials. |
Sustainability capabilities unlock analysis for new and existing products to accurately evaluate their environmental impact in terms of carbon footprint, energy use, and water consumption. |
What is Process Manufacturing?
Process manufacturing combines different raw materials and ingredients into a finished product through mixing, blending, and transformation methods like boiling or chemical reactions. Instead of units, this method creates end products measured in volume, like gallons of chemical solvent or quarts of juice.
The key elements of process manufacturing differ from discrete manufacturing in subtle ways:
- A recipe or formula and specialized BOMs define the ingredients that go into a process manufacturing product. The recipe also specifies the operations or techniques that will successfully combine the ingredients. Process manufacturing BOMs include specialized formats for R&D, layered product configurations, manufacturing, and site-specific applications.
- Manufacturing locations are roughly equivalent to work centers. They represent the location or station where the manufacturer performs a set of related tasks and operations. Examples include a brewery’s fermentation tanks or a set of batch reactors for pharmaceuticals.
- Unit of measurement conversions and scalability allow manufacturers to dial the quantity of an output up or down through relatively simple calculations.
- Safety data sheets provide essential information about hazardous chemicals and substances. They inform both the process manufacturers handling these substances and industrial end users, and they follow strict guidelines.
Outline of the Process Manufacturing Workflow
Process manufacturing echoes the stages of discrete manufacturing, but the individual steps differ in important ways.
A New Dish Detergent
To visualize process manufacturing, think of a household cleaning products provider formulating and creating a new, scentless dish detergent.
- Research and development: First, the R&D team experiments with different formulas to capture consumer preferences and ensure cost-effective production. This phase involves creating and refining the exact specifications for ingredients and their proportions.
- Regulatory compliance: The compliance team collaborates closely with R&D to check the proposed formulation against regulatory frameworks in the product’s target markets. Compliance software integrated into their PLM solution makes these checks relatively straightforward.
- Planning: The team forecasts demand and organizes resources and locations by determining raw materials, equipment, and production schedules.
- Procurement: Working with a roster of suppliers, the procurement team sources and purchases necessary ingredients. They consider overall price, quality control, and existing relationships. The dish soap’s elaborate mix of solvents, surfactants, stabilizers, and other ingredients requires an extensive network of suppliers—some international and some domestic.
- Production: At this point, manufacturing locations are ready to combine raw materials. Production includes two stages: mixing the ingredients and processing. During the processing stage, machines continuously heat and stir the solution to ensure they distribute the ingredients evenly.
- Quality control: Quality specialists test the detergent for consistency and quality by sampling batches and performing lab analyses to ensure it meets specifications.
- Packaging: The packaging team chooses clear vessels and minimal labels that showcase the clear, colorless, odorless liquid. The dish soap is ready for storage and distribution.
A Flow Chart for Process Manufacturing
How Process Manufacturers Use PLM Software
Process manufacturing software like Trace One Devex PLM can smooth the complexities and challenges that producers face. Supported by a suite of powerful modules, PLM software can help you maintain compliance, expedite time to market, and transform business processes.
Industry Challenge |
Trace One Solution |
Research and development is a time-consuming and labor-intensive process that can lead to dead ends and wasted effort. |
Trace One Devex PLM’s recipe management and product formulation capabilities let manufacturers automate recipe management, accelerate product development, and improve production quality. |
New product development and introduction (NPDI) involves complex planning and calculations across every aspect of a product, from ideation through planning and packaging. |
Trace One’s product development suite optimizes the entire NPDI process by making opportunities easier to discover, facilitating production and launch roadmaps, and simplifying packaging management and specifications. |
Supplier quality can be difficult to understand and maintain as global supply chains constantly shift and compound ingredients undergo changes associated with cost, availability, and compliance. |
Trace One Supplier Collaboration Portal (SCP) facilitates and simplifies qualification, registration, and management for suppliers and vendors to maintain quality, even as product formulations evolve. |
Product inconsistencies erode consumer trust and expose manufacturers and retailers alike to brand damage, regulatory penalties, and even lawsuits. |
Trace One Devex PLM’s built-in quality management tools provide end-to-end visibility and connectivity to get feedback to the right people and remedy any issues. |
Global food legislation adds layers of complexity for process manufacturers in the food and beverage industry, introducing an ever-changing set of compliance regulations in different regions and languages around the world. |
REGDATA®, Trace One’s global food regulatory database provides a robust repository with information on additives, flavoring substances, pesticides, and more to help you avoid compliance violations and recalls. |
Labeling requirements are strict and specific for chemical companies. Failure to comply with these rules can result in stiff fines, product recalls, or legal trouble related to illness and injury. |
Trace One SDS Authoring generates safety data sheets and hazard labels that align automatically with the Globally Harmonized System (GHS) to ensure compliance with global, regional, and local standards. |
Environmental sustainability operates within a delicate balance between manufacturing processes, business demands, regulatory requirements, and consumer perception. |
Trace One Sustainability helps manufacturers analyze new and existing formulas for environmental impact. Through integrated lifecycle assessment (LCA) analysis, companies can make sustainability decisions early in the product development cycle, saving time and preventing rework. |
Transforming Manufacturing Through PLM Solutions
PLM software helps both discrete and process manufacturers maintain compliance, expedite time to market, and transform business processes. Comprehensive, integrated solutions have the power to connect global teams, disparate systems, and siloed data to deliver successful products to market on time and on budget.
If you’re a process manufacturer or CPG retailer, find out how Trace One PLM solutions can revolutionize your workflows to make remarkable products happen.
Let’s Get in Touch
Connect with us to learn how Trace One can serve your organization’s unique needs.